Lupine
Publishers- Latest Trends in Textile and Fashion Designing
Abstract
During high speed sewing, needle thread is subjected to dynamic
loading, inertia forces, friction and repeated tensile stresses at
tremendous rates. The value of these stresses depends upon stitching
speed, sewing thread tension, stitch length and sewing thread
properties. These parameters affect the tensile properties of sewing
threads adversely, leading to loss in seam strength. In this study,
the effect of various parameters lubrication (%), stitch density, the
number of fabric layers and stitching speed on tensile properties
of sewing thread has been studied using Box- Behnken design. Contrary to
the popular belief, loss in tenacity increases as stitching
speed increases. 4% lubrication (%) is suggested to get minimum tenacity
loss (%).
Keywords: Breaking Elongation; Initial Modulus; Sewing Thread; Tenacity
Keywords: Breaking Elongation; Initial Modulus; Sewing Thread; Tenacity
Introduction
In the apparel industry, the sewing process is one of the
most critical processes in the determination of productivity
and quality of the finished garment Anand [1]. The production
rate of garment industry has increased significantly because of
technological development. Due to increase in the machine speed,
rapid modification in fabric characteristics just as fabric type, the
degree of finishing has brought more stringent requirements on the
characteristics and performance of threads used in garment industry
Gersak and Knez [2]. It is well established that manufacturers can
improve the quality of garments by using better sewing thread,
improved machinery, better garment design and trained personnel.
However, use of better-quality sewing thread appears to be easiest
and least expensive Rengasamy [3]. Seam strength and seam
performances are dependent on the strength of the threads. So,
high strength of sewing thread is a basic requirement for good
sewability Midha [4]. If thread becomes weaker during sewing
process and after getting incorporated into the seam it results into
lower seam strength.
The other tensile properties such as breaking elongation and
initial modulus also influence the quality of seam in different
ways. Therefore, it becomes very important to know the sewing
mechanism and extent of loss in tensile properties during sewing.
During the sewing process in a high-speed sewing machine,
the thread is subjected to complicated kinematic and dynamic
conditions. Sewing thread is subjected to friction, tensile, bending,
compressive, shear, and surface stresses. These stresses act on
the thread frequently for an adequately prolonged period of time;
sewing thread passes more than 50-80 times through the fabric, the
needle eye, and bobbin case mechanism before getting incorporated
into the seam Ukponmwan [5], Midha [6]. As a result, both the
sewing thread and the yarns in the fabric get abraded during the
sewing process. Number of researchers observed that there could
be 30-40% strength reduction in the cotton thread after sewing
Sundaresan [7], Sundaresan [8]. Different studies confirm that
structural damages in the thread, results due to the displacement
of the plies, twist alterations at specific locations and the surface
fibres get pulled out of the structure. The damages are mostly
concentrated at the interlocking portion of the needle thread in
the stitch, where maximum tension, bending and thread-thread
abrasion takes place Sundaresan [7], Rudolf and Gersak [9]. Most
of the researchers focused on estimating the amount of damage in
the sewing threads during sewing and identified the various reason
for that damage viz. structural damage, dynamic loading, and
thermal damage. However, limited studies are available on the role
of different parameters affecting the loss in thread strength after
sewing. A careful selection of these parameters can help in reducing
the damage in sewing threads during sewing. In this paper, the effect of
process parameters like lubrication (%), stitch density,
the number of fabric layers and machine speed has been studied
on changes in the tensile properties (tenacity, breaking elongation,
and initial modulus) of the needle threads during sewing.
The other tensile properties such as breaking elongation and initial modulus also influence the quality of seam in different ways. Therefore, it becomes very important to know the sewing mechanism and extent of loss in tensile properties during sewing. During the sewing process in a high-speed sewing machine, the thread is subjected to complicated kinematic and dynamic conditions. Sewing thread is subjected to friction, tensile, bending, compressive, shear, and surface stresses. These stresses act on the thread frequently for an adequately prolonged period of time; sewing thread passes more than 50-80 times through the fabric, the needle eye, and bobbin case mechanism before getting incorporated into the seam Ukponmwan [5], Midha [6]. As a result, both the sewing thread and the yarns in the fabric get abraded during the sewing process. Number of researchers observed that there could be 30-40% strength reduction in the cotton thread after sewing Sundaresan [7], Sundaresan [8]. Different studies confirm that structural damages in the thread, results due to the displacement of the plies, twist alterations at specific locations and the surface fibres get pulled out of the structure. The damages are mostly concentrated at the interlocking portion of the needle thread in the stitch, where maximum tension, bending and thread-thread abrasion takes place Sundaresan [7], Rudolf and Gersak [9]. Most of the researchers focused on estimating the amount of damage in the sewing threads during sewing and identified the various reason for that damage viz. structural damage, dynamic loading, and thermal damage. However, limited studies are available on the role of different parameters affecting the loss in thread strength after sewing. A careful selection of these parameters can help in reducing the damage in sewing threads during sewing. In this paper, the effect of process parameters like lubrication (%), stitch density, the number of fabric layers and machine speed has been studied on changes in the tensile properties (tenacity, breaking elongation, and initial modulus) of the needle threads during sewing.
Materials and Methods
Cotton staple spun threads of 37tex with silicon and wax finish
are used in the study. The threads are two and ply and shows 314
turns per meter. The physical properties of the sewing threads are
shown in Table 1. The effect of various process parameters, viz.
lubrication (%), number of fabric layers, stitch density and stitching
speed on the tensile properties of sewing threads is studied by
measuring the tensile properties of the threads before and after
sewing at three different levels of these parameters, according to
Box-Behnken experimental design (Tables 2-3). Brother Industrial
lockstitch sewing machine is run at different speeds for preparation
of samples using rib knitted fabric. Tensile testing of the needle
threads before and after sewing is done at a gauge length of 250mm
on Universal Testing Machine as per ASTM D 2256. Thirty tests are
carried out for individual sample and the error is found to be less
than 4% at 95% confidence limit. The change in tensile properties
is calculated using equation 1.
Box Behnken Design.
Loss(%)=(Tensile property before sewing-Tensile property
after sewing)/(Tensile property before sewing)×100
In order to study the individual and interactive effect of each
parameter on tensile properties, response surface regression
equations are developed for loss in tensile properties at different
levels of lubrication (%), number of fabric layers, stitch density and
stitching speed by backward elimination method.
Box Behnken Design.
Loss(%)=(Tensile property before sewing-Tensile property after sewing)/(Tensile property before sewing)×100
In order to study the individual and interactive effect of each parameter on tensile properties, response surface regression equations are developed for loss in tensile properties at different levels of lubrication (%), number of fabric layers, stitch density and stitching speed by backward elimination method.
Results and Discussion
Table 4 shows the tenacity loss, breaking elongation loss
and initial modulus loss after sewing at different levels of the
parameters. The average of 30 readings for each sample is analyzed
to create regression equation on statistical software STATISTICA
8. The linear and polynomial equations are tried along with the
interaction of the parameters, at 95% confidence level. The bestfit
equations for tenacity loss, breaking elongation loss and initial
modulus loss are generated. The regression equations have a very
good R2 value and can be used to study the effect of different
parameters on tenacity loss, elongation loss and initial modulus
loss.
*-ve sign indicates gain in initial modulus.
*-ve sign indicates gain in initial modulus.
Tenacity loss and breaking elongation loss
Analysis of variance shows lubrication %, stitch density and
stitching speed has a significant effect on the tenacity loss (Table
5), whereas number of fabric layers does not show any significant
effect on the tenacity loss. However, number of fabric layers and
stitching speed has an interactive effect on tenacity loss. Breaking
elongation is affected by number of fabric layers and machine speed.
Lubrication % and stitch density does not show any significant
effect on breaking elongation loss (Table 5).
Figure 1 shows the effect of lubrication% and stitch density on
tenacity loss (%) of thread during sewing. It is observed that, as
the lubrication % increases, the loss in tenacity first decreases and
then increases. This is because lubricants provide a surface coating
to sewing threads that protect it from the abrasive actions during
its interaction with machine parts, fabric and bobbin thread. But
further increase in lubrication ratio causes decreases in fibre to
fibre friction which leads to slippage during the tensile loading and
therefore reflects as tenacity loss (%). Lubrication % does not show
any significant effect on the elongation loss% as shown in Figure
2. This may be due to the increased slippage of fibres at higher
lubrication, leading to increase in breaking elongation, which
compensates for the loss in breaking elongation during the sewing
process.
Further, it is observed that tenacity loss first decreases and
then increases with increase in stitch density as shown in Figure 1.
Increased level of stitch density causes a decrease in stitch length,
thereby decreasing thread consumption per stitch. The stress level
experienced by the thread during pulling of the thread from the
spool during stitch tightening is reduced and therefore, the threads
experience a lower level of damage. At higher stitch density, the
thread also experiences a higher number of dynamic loading and
abrasive cycles before getting incorporated into the fabric, leading
to more damage to the thread. As the stitch density increased
further, the effect of a higher number of loading and abrasive cycles
outweighs the effect of decreased stress levels, and therefore the
thread experiences higher tenacity loss Midha and Gupta [10].
Stitch density does not show any effect on the elongation loss of
sewing threads as shown in Figure 2.
Figure 3 shows the effect of stitching speed and number of
fabric layers on tenacity loss of sewing thread. It is observed that
number of fabric layers does not show a notable effect on tenacity
loss (%) as per analysis of variance (Table 5). However, number of
fabric layers and stitching speed have an interactive effect on the
tenacity loss (Figure 3).
Figure 3: Effect of number of fabric layers and stitching
speed on tenacity loss (%) of sewing thread.
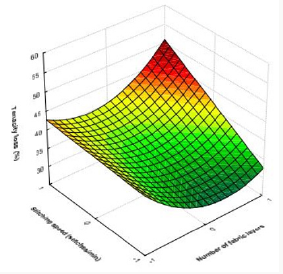
Figure 1 shows the effect of lubrication% and stitch density on tenacity loss (%) of thread during sewing. It is observed that, as the lubrication % increases, the loss in tenacity first decreases and then increases. This is because lubricants provide a surface coating to sewing threads that protect it from the abrasive actions during its interaction with machine parts, fabric and bobbin thread. But further increase in lubrication ratio causes decreases in fibre to fibre friction which leads to slippage during the tensile loading and therefore reflects as tenacity loss (%). Lubrication % does not show any significant effect on the elongation loss% as shown in Figure 2. This may be due to the increased slippage of fibres at higher lubrication, leading to increase in breaking elongation, which compensates for the loss in breaking elongation during the sewing process.
Further, it is observed that tenacity loss first decreases and then increases with increase in stitch density as shown in Figure 1. Increased level of stitch density causes a decrease in stitch length, thereby decreasing thread consumption per stitch. The stress level experienced by the thread during pulling of the thread from the spool during stitch tightening is reduced and therefore, the threads experience a lower level of damage. At higher stitch density, the thread also experiences a higher number of dynamic loading and abrasive cycles before getting incorporated into the fabric, leading to more damage to the thread. As the stitch density increased further, the effect of a higher number of loading and abrasive cycles outweighs the effect of decreased stress levels, and therefore the thread experiences higher tenacity loss Midha and Gupta [10]. Stitch density does not show any effect on the elongation loss of sewing threads as shown in Figure 2.
Figure 3 shows the effect of stitching speed and number of fabric layers on tenacity loss of sewing thread. It is observed that number of fabric layers does not show a notable effect on tenacity loss (%) as per analysis of variance (Table 5). However, number of fabric layers and stitching speed have an interactive effect on the tenacity loss (Figure 3).
Figure 3: Effect of number of fabric layers and stitching
speed on tenacity loss (%) of sewing thread.
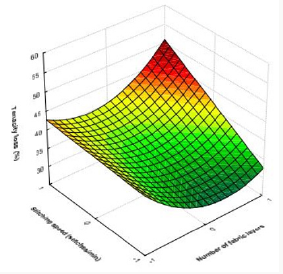
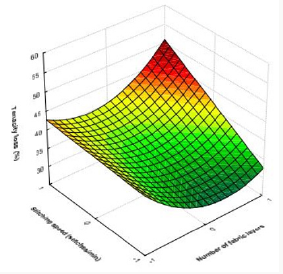
Effect of number of fabric layers and stitching speed on tenacity loss (%) of sewing thread
Figure 3 At lower stitching speed, as the number of fabric layers
increase, tenacity loss decreases. But at higher machine speed as
the number of fabric layers increase, a sharp increase in tenacity
loss is observed. As number of fabric layers increase, the thread
consumption per stitch increases. Increased thread consumption
per stitch means the needle thread is subjected to a lower number
of loading cycles before getting incorporated into the seam; which
in turn leads to lower damage to the sewing thread. However, as the
number of fabric layers increases further, the needle penetration
force increases and sewing thread is subjected to higher abrasive
damage. Higher abrasive damage of cotton fibers outweighs the
effect of lower number of loading cycles, and therefore an increase
in tenacity loss (%) is observed Midha [6].
Similarly, as stitching speed increases, at lower number of
fabric layers, the marginal increase in tenacity loss is observed.
But tenacity loss significantly increases, as the stitching speed
increases, at higher number of fabric layers. As the stitching speed
and number of fabric layers increase, higher penetration forces and
higher frequency causes increase in needle temperature, which is
expected to damage the synthetic threads. However, in the present
study cotton thread has been used. As stitching speed increases,
needle thread has more frequent interaction with various stresses
imposed during sewing and therefore visco-elastic characteristics
of the thread are affected. After dynamic loading of the thread
at higher levels of tighening tension, the sewing thread is held
retracted for stress recovery for a very short time and therefore is
not able to attain stress relaxation. Due to this, stress in the sewing
thread increases as the number of cycles increase. Consequently,
extension of lateral molecular bonds and molecular slippage results
in the breakage of these bonds.
Figure 4 shows the effect of stitching speed and number of fabric
layers on elongation loss (%). Number of fabric layers and stitching
speed have an interactive effect on the elongation loss (Table 5).
At lower stitching speed, as the number of fabric layers increase,
elongation loss increases. But at higher stitching speed as the
number of fabric layers increase, no significant elongation loss (%)
is observed. But, when both the parameters considered separately
then they have notable effect on elongation loss (Figure 4) and
increasing trend is observed. As the number of layers increases,
abrasion between needle thread and fabric also increases. Due to
this surface of the sewing thread get damaged ultimately causing
higher elongation loss (%). The same trend is observed for stitching
speed. As machine speed increases, due to frequent contact of
needle thread with fabric, fibres get pulled out from thread surface.
So, elongation loss increases.
Figure 5 shows the effect of lubrication on the loss of initial
modulus. As lubrication % increases from 3 to 4%, there is an
increase in initial modulus loss after sewing. Because silicone oil
lubricates the fiber surface and causes twist to unravel, leading
to pullout of fibres from the structure of the thread. At higher
lubrication %, initial modulus loss decreases. Initial modulus is
known to increase after the dynamic loading of threads, whereas
it decreases during the passage through the needle and fabric, and
during bobbin thread interaction. The abrasive effect outweighs
the increase during the dynamic loading, leading to fall in initial
modulus after sewing. At higher lubrication %, the abrasive damage
is expected to reduce and therefore a small increase in initial
modulus due to dynamic loading, causes lower initial modulus loss.
The results are similar to what has been observed by the previous
researchers [6,8,10]. Further, it is observed from the analysis of
variance that stitch density does not show any significant influence
over initial modulus loss%.
Figure 6: Effect of number of fabric layers and stitching
speed on initial modulus loss (%) of sewing thread.
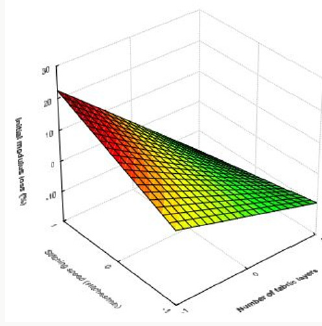
Figure 6 shows the effect of stitching speed and number of
fabric layers on initial modulus loss of sewing thread. The effect of
stitching speed on the initial modulus loss % is observed to have
an interactive effect with the number of fabric layers (Table 5). At
lower stitching speed, as number of fabric layers increase initial
modulus loss slightly decreases. But at higher stitching speed, a
significant drop in initial modulus loss takes place. The loss in
initial modulus occurs due to the non-contribution of surface fibres
to thread tension. Number of abrasive cycles cause fraying of thread
surface and pull out of fibres, leading to a loss in initial modulus of
threads. As the number of fabric layers increases, the number of
abrasive cycles decrease, but the stress levels to which the thread
is exposed during tightening is higher. With an increase in machine
speed, surface of the thread gets damaged and fibres from the
surface come out and that contribute to the initial modulus loss %.
Similarly, as stitching speed increases, at lower number of fabric layers, the marginal increase in tenacity loss is observed. But tenacity loss significantly increases, as the stitching speed increases, at higher number of fabric layers. As the stitching speed and number of fabric layers increase, higher penetration forces and higher frequency causes increase in needle temperature, which is expected to damage the synthetic threads. However, in the present study cotton thread has been used. As stitching speed increases, needle thread has more frequent interaction with various stresses imposed during sewing and therefore visco-elastic characteristics of the thread are affected. After dynamic loading of the thread at higher levels of tighening tension, the sewing thread is held retracted for stress recovery for a very short time and therefore is not able to attain stress relaxation. Due to this, stress in the sewing thread increases as the number of cycles increase. Consequently, extension of lateral molecular bonds and molecular slippage results in the breakage of these bonds.
Figure 4 shows the effect of stitching speed and number of fabric layers on elongation loss (%). Number of fabric layers and stitching speed have an interactive effect on the elongation loss (Table 5). At lower stitching speed, as the number of fabric layers increase, elongation loss increases. But at higher stitching speed as the number of fabric layers increase, no significant elongation loss (%) is observed. But, when both the parameters considered separately then they have notable effect on elongation loss (Figure 4) and increasing trend is observed. As the number of layers increases, abrasion between needle thread and fabric also increases. Due to this surface of the sewing thread get damaged ultimately causing higher elongation loss (%). The same trend is observed for stitching speed. As machine speed increases, due to frequent contact of needle thread with fabric, fibres get pulled out from thread surface. So, elongation loss increases.
Figure 5 shows the effect of lubrication on the loss of initial modulus. As lubrication % increases from 3 to 4%, there is an increase in initial modulus loss after sewing. Because silicone oil lubricates the fiber surface and causes twist to unravel, leading to pullout of fibres from the structure of the thread. At higher lubrication %, initial modulus loss decreases. Initial modulus is known to increase after the dynamic loading of threads, whereas it decreases during the passage through the needle and fabric, and during bobbin thread interaction. The abrasive effect outweighs the increase during the dynamic loading, leading to fall in initial modulus after sewing. At higher lubrication %, the abrasive damage is expected to reduce and therefore a small increase in initial modulus due to dynamic loading, causes lower initial modulus loss. The results are similar to what has been observed by the previous researchers [6,8,10]. Further, it is observed from the analysis of variance that stitch density does not show any significant influence over initial modulus loss%.
Figure 6: Effect of number of fabric layers and stitching
speed on initial modulus loss (%) of sewing thread.
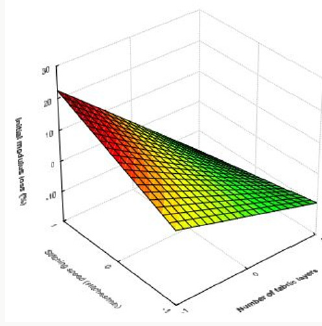
Figure 6 shows the effect of stitching speed and number of
fabric layers on initial modulus loss of sewing thread. The effect of
stitching speed on the initial modulus loss % is observed to have
an interactive effect with the number of fabric layers (Table 5). At
lower stitching speed, as number of fabric layers increase initial
modulus loss slightly decreases. But at higher stitching speed, a
significant drop in initial modulus loss takes place. The loss in
initial modulus occurs due to the non-contribution of surface fibres
to thread tension. Number of abrasive cycles cause fraying of thread
surface and pull out of fibres, leading to a loss in initial modulus of
threads. As the number of fabric layers increases, the number of
abrasive cycles decrease, but the stress levels to which the thread
is exposed during tightening is higher. With an increase in machine
speed, surface of the thread gets damaged and fibres from the
surface come out and that contribute to the initial modulus loss %. 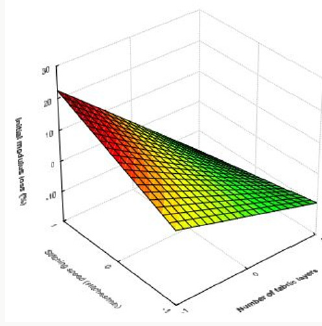
Conclusion
In the present investigation, the effect of lubrication %, number
of fabric layers, stitch density and stitching speed on the loss in
tensile properties of cotton sewing threads after sewing has been
studied. The regression equations for various responses agree
well with the experimental data as indicated by higher values of
coefficient of determination. It is observed that lubrication %, stitch
density and stitching speed has a significant effect on the tenacity
loss. Elongation loss % is affected by lubrication % and number
of fabric layers. Initial modulus is affected by all the parameters
except stitch density. Number of fabric layers and stitching speed
have an interactive effect on loss of all tensile properties.
For more Lupine
Publishers Open Access Journals Please visit our
website:
For more Open Access Latest Trends in Textile and Fashion Designing Journal articles Please Click Here:
Follow on Linkedin : https://www.linkedin.com/company/lupinepublishers
Follow on Twitter : https://twitter.com/lupine_online
For more Lupine
Publishers Open Access Journals Please visit our
website:
For more Open Access Latest Trends in Textile and Fashion Designing Journal articles Please Click Here:
Follow on Linkedin : https://www.linkedin.com/company/lupinepublishers
Follow on Twitter : https://twitter.com/lupine_online
No comments:
Post a Comment